Данный пост познакомит вас с тем, как делаются пластиковые окна.
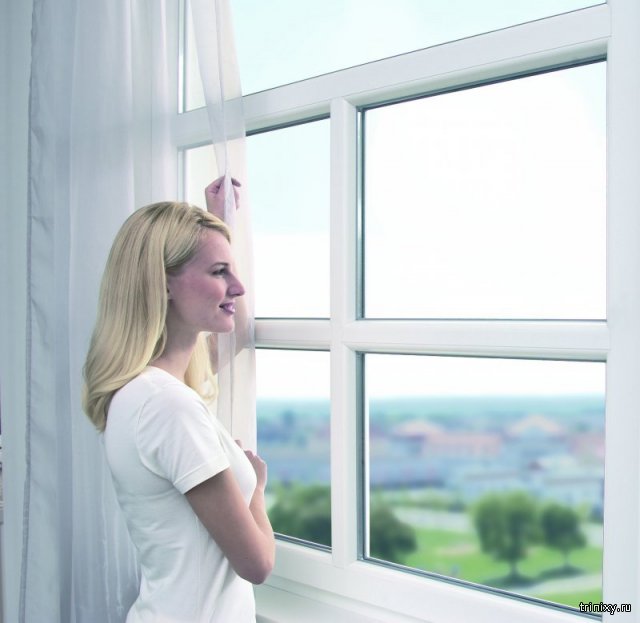
И так, приступим помолясь)))
В прошлый раз я показывал, как делаются стеклопакеты, но сейчас мы их почти не делаем, выгодней заказывать в конторах, которые занимаются чисто изготовлением этих пакетов, у них другое оборудование и другие объёмы, поэтому тягаться с ними, в экономическом плане не вариант. Себестоимость их продукции получается в разы ниже. Поэтому основная моя специальность-это сборщик конструкций ПВХ. И хоть начинал я работать со стеклом, но время заставило освоить другие специальности на данном производстве.
Фотоаппарат у меня всё тот же, так что за качество фото извиняюсь ещё раз. Ну и писарь я ещё тот, так что и за ошибки сильно не пинайте)))
Все размеры в миллиметрах. Я писал об этом, но давайте поясню почему, потому что допуски идут именно в миллиметрах. Казалось бы, ну что такого, один миллиметр, ан нет, из-за него окно может просто не работать, или будет продувать.
Как говорил один человек, который раньше работал у нас: наша работа нести свет и тепло людям! И я согласен с ним. Но то что людям тепло и светло, для работников такого производства каждодневный тяжёлый труд. Работа физически тяжёлая и очень нудная. Пожалуй каждодневные операции, не отличающиеся разнообразием, гораздо тяжелей, чем постоянная таскание окон с места на место.
Так, чего то меня не в ту степь понесло))))
Возвращаемся к нашему шашлыку, ой, не то. К баранам. Блин, тоже убежал. А, к окнам возвращаемся.
Любая работа, на любом производстве, начинается с чертежей или эскизов выпускаемой продукции. После замеров и подсчётов, делается распечатка окна и присылается из офиса в цех.
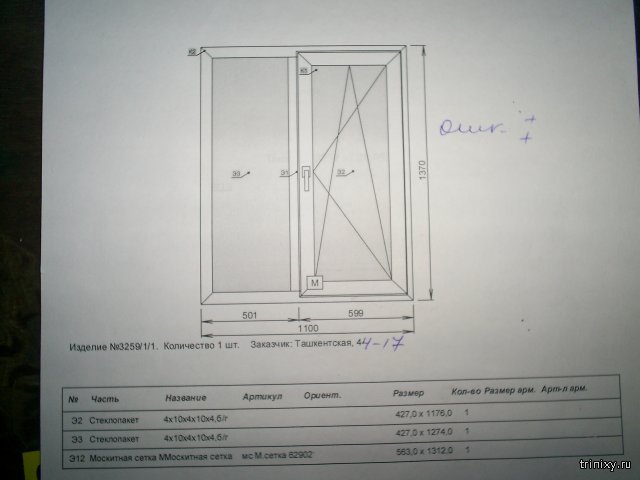
Вообще программа должна считать всё полностью, железо, створку и прочее, прочее. Но в этом случае на одно окно будет распечатка в несколько листов. А это не совсем удобно при нарезке, перебирать все эскизы чтоб отыскать, что резать в первую очередь ещё тот гемор. По-этому я выписываю их на один листок и режу уже с него.
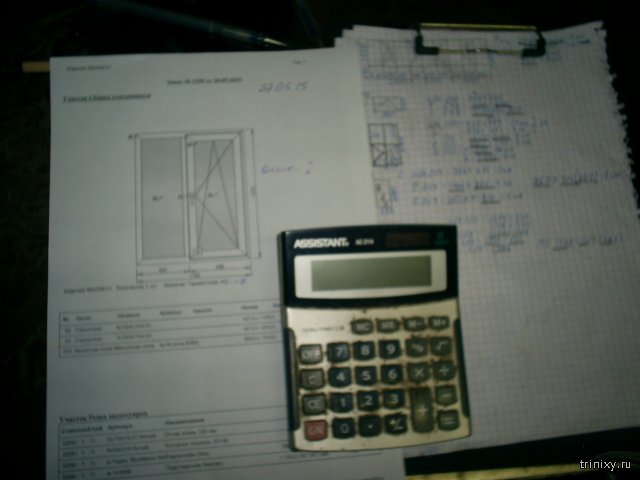
Мучить расчётами о бьяснениями к ним я вас не буду, у нас тут не урок математики. Да и зачем вам знание того, как высчитывается створка между импостами, или между рамой и импостом? Думаю в жизни оно вам не пригодится. Но если кому то будет интересно, то пишите, объясню.
Вот башка лысая, совсем забыл! Операций тут гораздо больше, чем при изготовлении пакетов, поэтому в один пост не уложусь, допишу в следующий выходной)))
И так, она звалась Татьяной...
Весь пластик приходит палками длинной 6500, и только потом уже нарезается на нужные размеры.
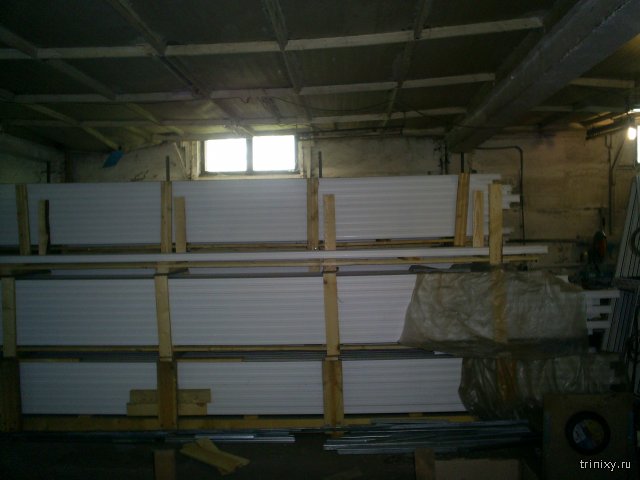
Весь пластик идёт трёх видов: рама, створка, импост.
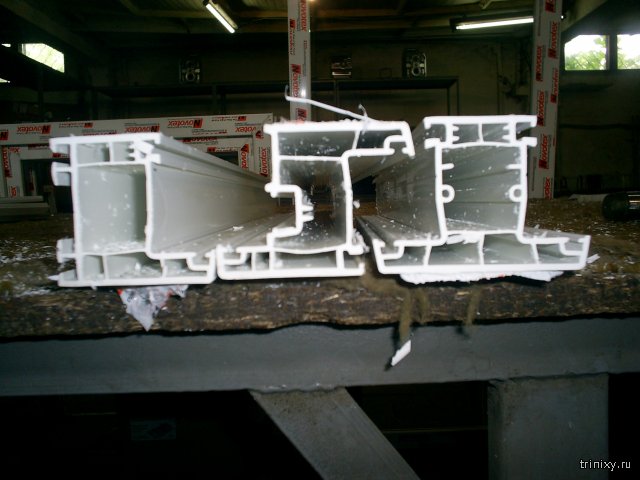
Думаю с рамой и створкой всё понятно. Давайте разберёмся с импостом. Поскольку стандартный размер окна 1400*1300, то делать створку во всё окно можно конечно, но она будет некорректно работать, из-за большого веса, что будет требовать постоянной регулировки. Чтобы уменьшить створку и нужен импост, он разделяет окно на части, что соответственно уменьшает створку, делая её легче.
И немного интересной инфы. Импост в переводе с португальского-налог.
А у нас в цеху есть такой прикол, если у кого то болит что то, особенно спина, предлагается сделать импостотерапию, а именно огреть широкой частью импоста по хребтине)))))
И так, возвращаемся к нашим баранам. Тьфу ты, что то меня всё на шашлык тянет.)))
Возвращаемся к нарезке.
Нарезаем пластик на нужные куски: рама, створка зарезаются под 45 градусов(почти водка), импост режется прямо.
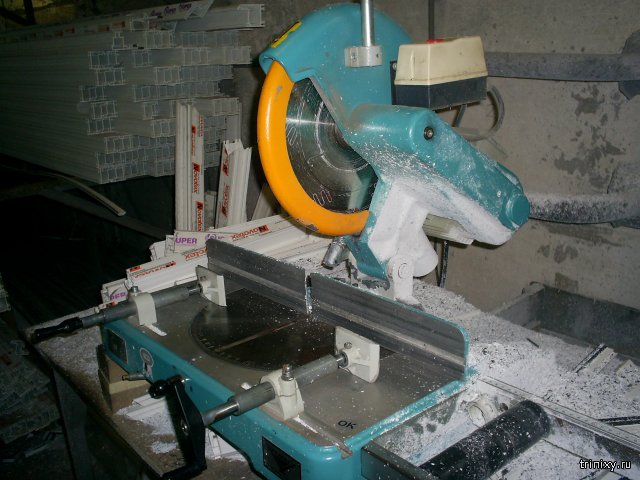
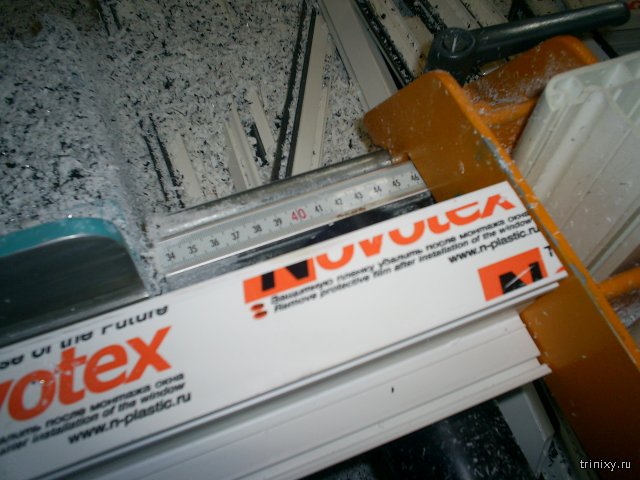
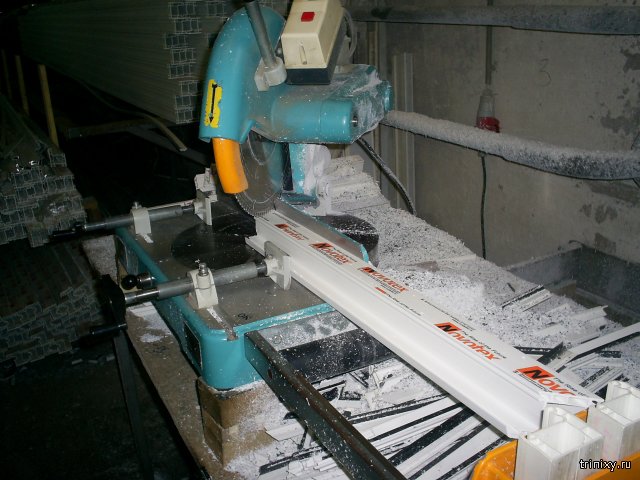
Поскольку заказав бываем много, а все размеры у них разные, то чтоб не перепутать окна при следующих операциях, помечаем нарезку маркером.
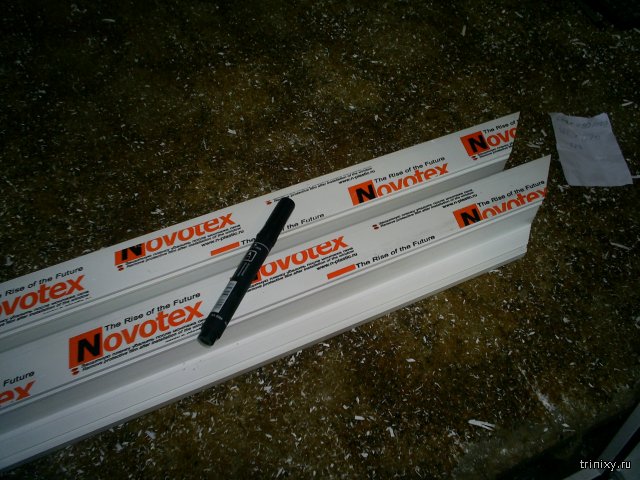
Поскольку пластик он и есть пластик, и что бы его не выгибало при дальнейшей сборки и установки, внутрь вставляется армирующий профиль. Он тоже идёт длинными палками, поэтому тоже сначала его нарезаем.
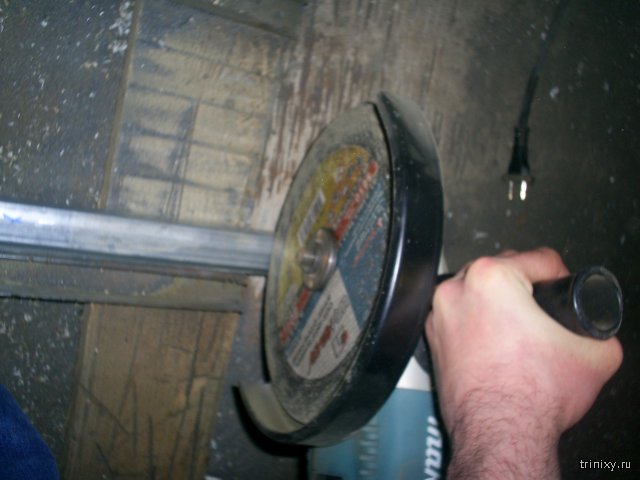
Надеюсь голова не закружилась от ракурса фото))))
Фрезеруем импост. Это нужно для того, что бы часть импоста не упиралась в борт рамы при дальнейшей сборке.
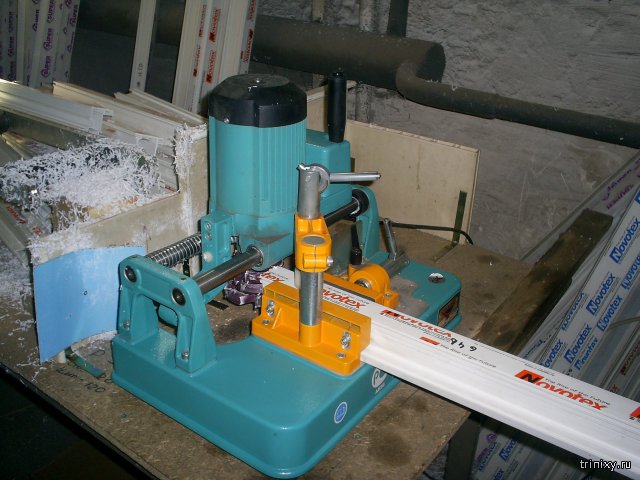
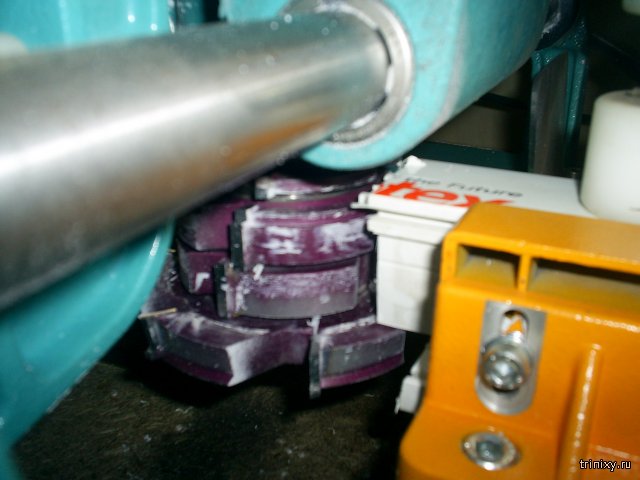
Вставляем армировку в готовую нарезку и прикручиваем к пластику.
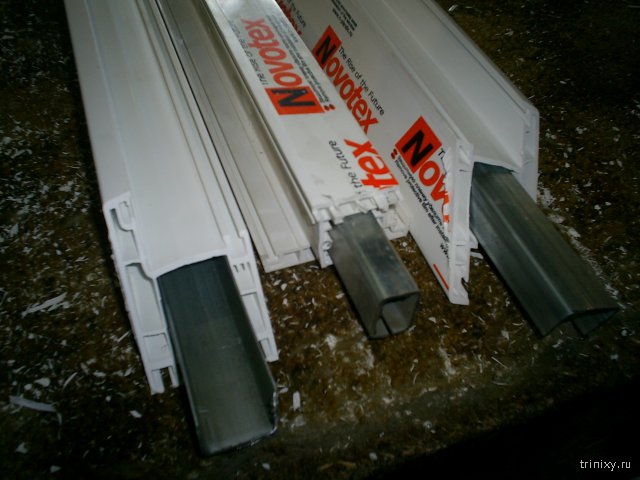
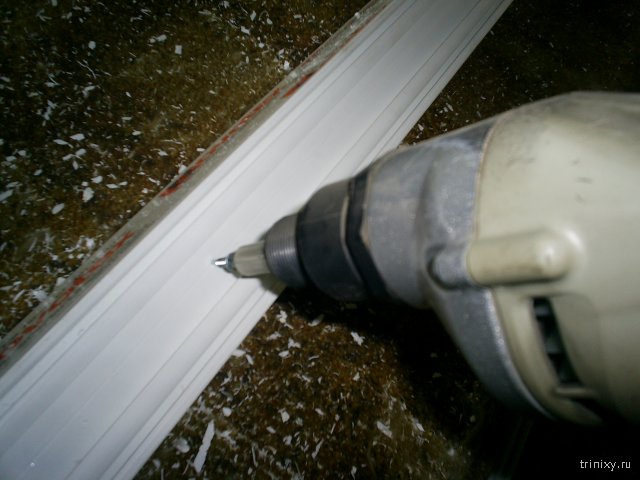
А к импосту прикручиваем дополнительное механическое соединение, или подпятники, как мы их называем. Прикручиваем с обоих сторон.
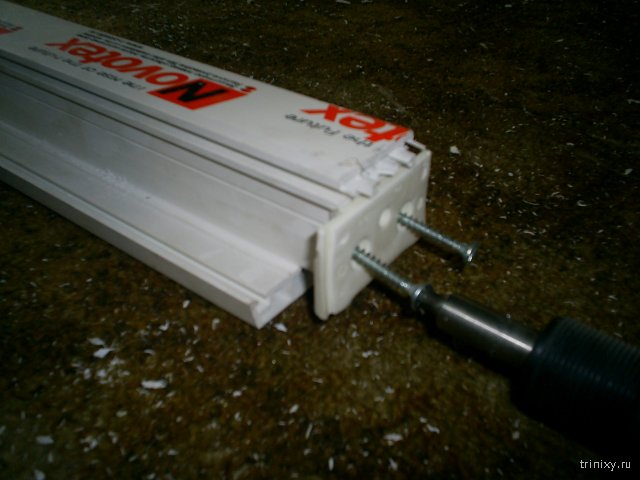
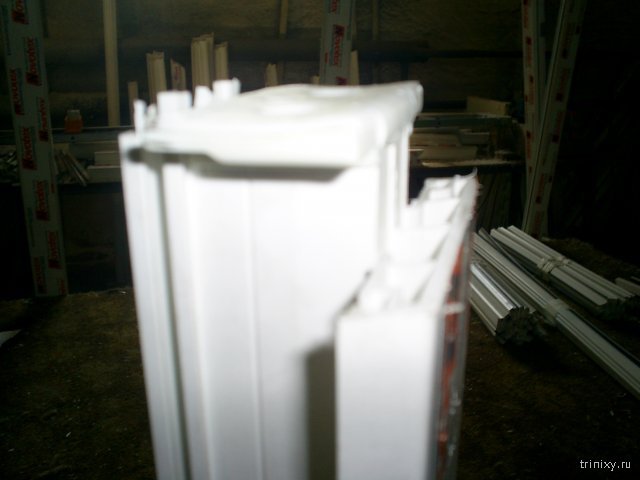
Прежде чем приступить к сварке, фрезеруем створку под ручку и замок.
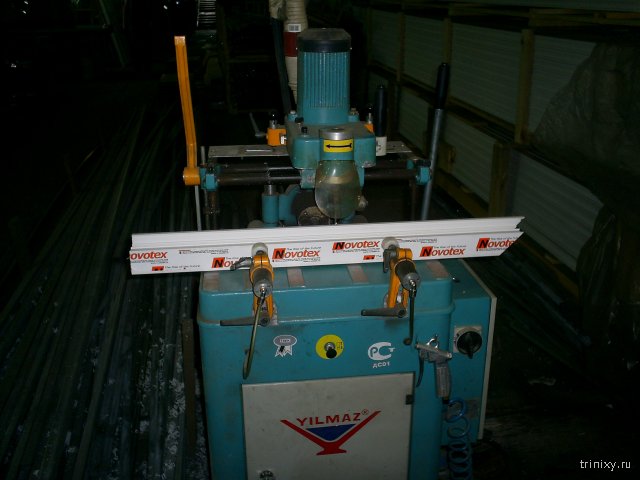
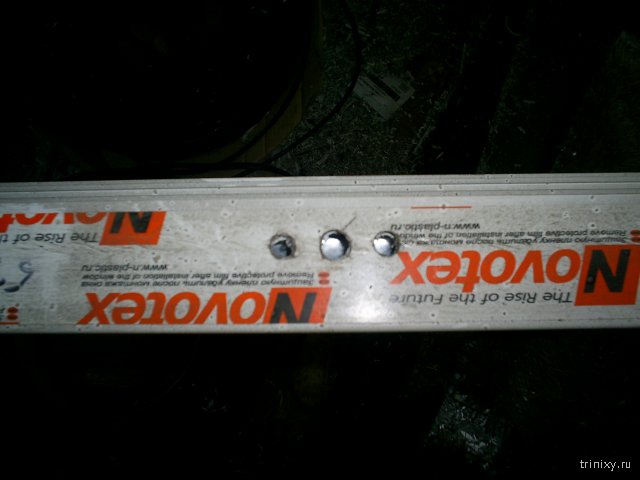
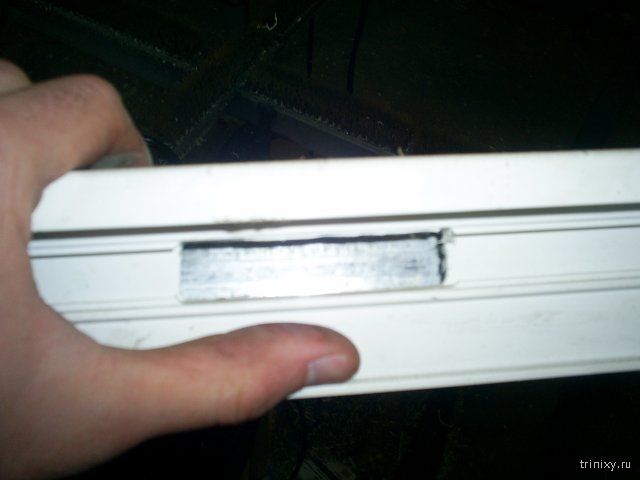
Подготовили пластик. И прежде чем варить обдуваем воздухом для того, чтоб внутри пластика не осталось никакого мусора. И опять же, чтоб при сварке мусор не налипал на тефлон, что приводит его к быстрому износу.
Не, сковородой с тефлоновым покрытием мы ещё пользоваться не научились. А жаль, станки очень дорогие)))
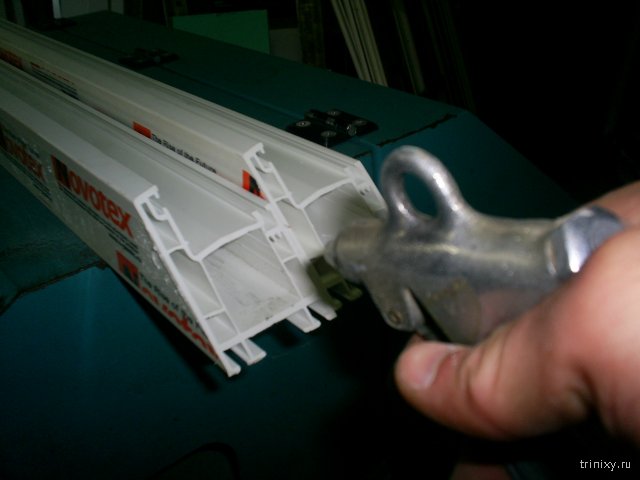
Ну а теперь приступаем к сварке. Или к пайке, тут кто как называет.
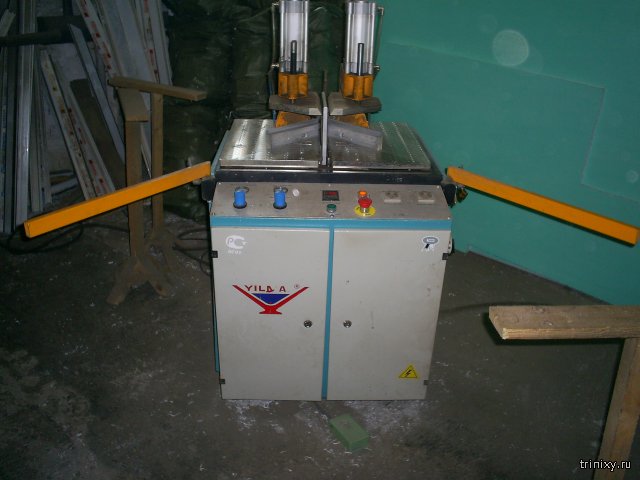
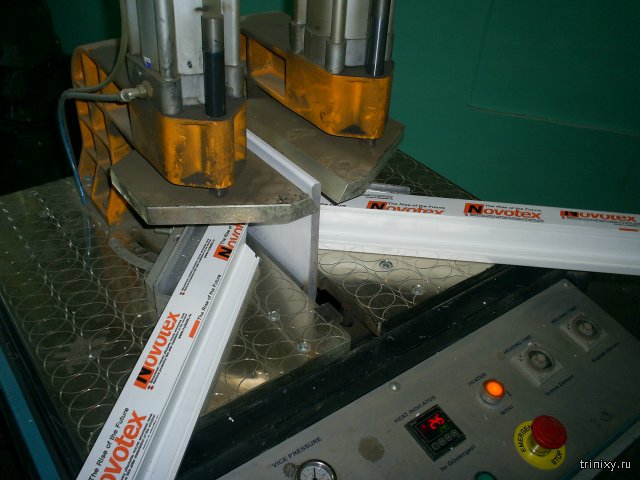
Упс, надеюсь никто не заметит моей невинной шалости))))
Пластик плавиться при температуре 245 градусов, а потом сжимается станком друг с другом, что обеспечивает плотное соединение. Но в этом случае остаются наплывы, которые зачищаем на другом станке.
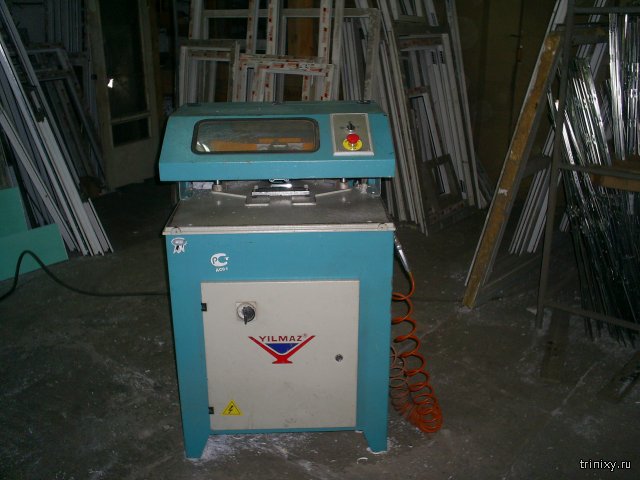
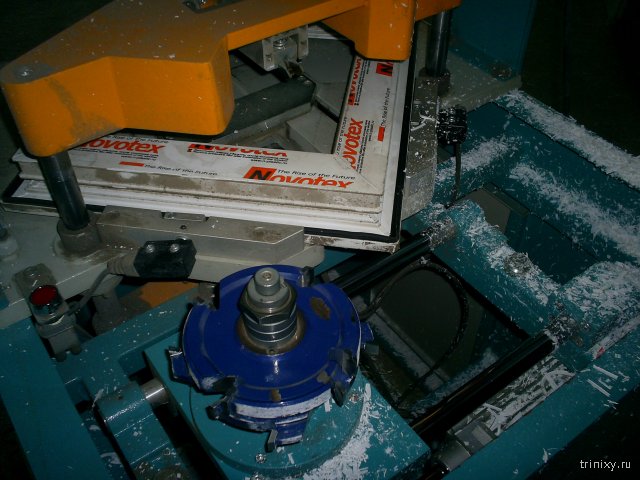
Когда я делал эти фотки, лет пять назад, то просто забыл сфоткать наплывы от сварки, поэтому как то так. Ну и конечно на раму и створку идут свои фрезы. На данной фотке фреза для створки. Для рамы фреза отличается меньшими размерами.
Зачищают они только наружние части, внутренние, куда вставляется резина зачищаем вручную, старой доброй стамеской.
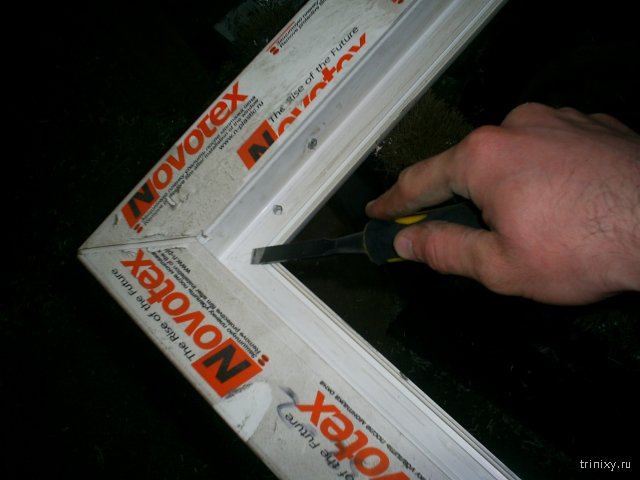
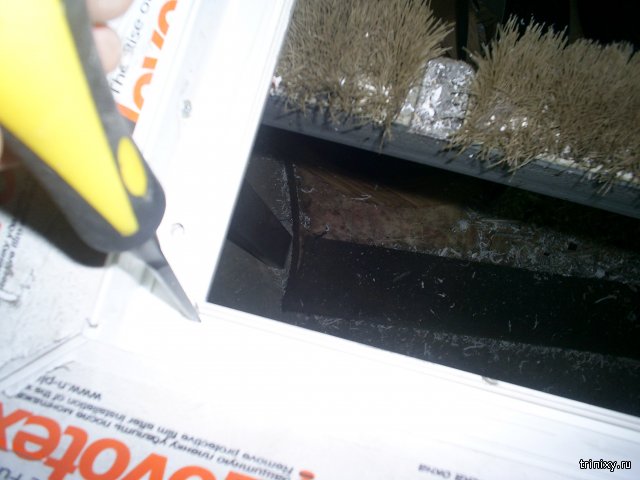
Подготовка закончена. Следующий этап-сборка.
Но о ней я расскажу уже через неделю. Так что продолжение следует...
А на сегодня всё. Всем лёгкой работы, и хорошей оплаты своего труда.
Был на производстве профиля и производстве (сборке) окон компаний ВЕКА и МастерБилл.
То, что здесь в посте - дичь конкретная.
И почему бы вам не сделать пост про то, чем вы занимаетесь? Не спорю, может будет интересней